Boru kaynağı: teknoloji ve bağlantı türleri
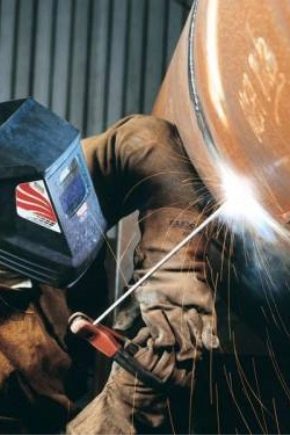
Günümüzde sanayi kuruluşlarında ve ev içi yaşamda boru hattı kurulumu yapılmadan yapılamaz. Materyalleri ve boru çapının büyüklüğünü göz önünde bulundurarak elementleri farklı yollarla bağlanır, ancak kaynak özellikle popülerdir. Bu yöntem, parçaları herhangi bir konumda sabitlemenizi sağlar ve en kolay ve en ucuz olarak kabul edilir, sıkı ve yüksek kaliteli yerleştirme sağlar.
Özel özellikler
Kaynak, boru hattının metal, plastik, beton ve seramikten yapılmış bağlantı parçalarının evrensel bir görünümüdür. Boru hattı, petrol, gaz, su ve diğer maddelerin taşınmasında kullanılan mühendislik iletişimi olduğundan, parçalarını doğru ve güvenli bir şekilde bağlamak önemlidir.Kaynak, bu görevlerle iyi çalışır, bu yüzden genellikle büyük çaplı paslanmaz çelik boruların, flanşların veya titanyum alaşımlarının kullanıldığı sondaj delikleri, kanalizasyon, endüstriyel ve proses hatlarının montajı sırasında seçilir.
Bu teknoloji aynı zamanda çeşitli çaplarda plastik, krom kaplı boruların birleştirilmesi için de uygundur. Hem küçük hem de büyük boru hatlarının tüm unsurları, Devlet Standartlarının düzenlemelerine uygun olarak belirlenmiş standartlara göre sabitlenmiştir.
Kurulumun özelliklerine ve dikişin köküne bağlı olarak, belirli bir sıcaklık ve kaynak tipi seçilir. Butt termal teknolojisi, boruların kenarlarını ısıtmaya dayanır, termomekanik, kaynaklı telin ısıtılmasıyla kaynatma parçalarıyla karakterize edilir. Mekanik görünüm, yatay boruların sürtünme ile sabitlenmesinde kullanılır. Soğuk kaynaklarda ise, parçaların sağlam ve güvenilir bir dikiş sağlayan bir kimyasal bileşim ile işlenmesiyle gerçekleştirilir.
Kaynaklamanın ana özelliği, uygulanması için boru uçlarının merkezlenmesini kolaylaştıran cihazlar olan merkezileştiricileri kullanmalarıdır. Merkezileştiriciler sayesinde iş hızlı ve dikişler yüksek kalitededir.
Kaynak avantajları aşağıdaki noktaları içerir:
- metal tasarrufu ve iş maliyeti;
- döküm ve dövme için mükemmel bir alternatif;
- çeşitli boyutlardaki boruları bağlama yeteneği;
- yüksek kalite ve sızdırmazlık; uygulama kolaylığı.
Dezavantajlara gelince, metalin deformasyonu sırasında mümkündür.
Araçlar ve ekipman
Kaynak en uygun ve en yaygın boru bağlantı şeklidir. Bağlantı parçaları sadece belirli bir deneyimi değil aynı zamanda anahtarlama modlarına sahip özel bir cihaz gerektirir. Böyle bir makine hem elektrik hem de gazla çalıştırılabilir ve ayrıca tasarımında bir soket kaynak cihazı da içerebilir. Boruların ev tipi füzyonu için birçok usta ayrıca invertör ile donatılmış bir makineye sahip olmayı tercih eder. Düzenlenen malzeme ve enerji tüketimine göre, cihazlar kontrol devreleri ile donatılmıştır.
İşin karmaşıklığına ve boru çapına bağlı olarak uygun ekipman seçilir.
elektrotlar
Çoğu durumda, kaynak için elektrotlar kullanılır. Büyük çaplı boruları yerleştirmek istiyorsanız, selüloz filmle kaplı elektrotları seçin.Köşe dikişlerinin oluşumu için genellikle rutil kaplamalı ürünler tercih edilir. Karmaşık pişirme planlandığında, daha sonra kombine (selüloz-rutil) elektrotlar kullanılır. En yaygın olanları UONI 13/55 ile kaplanan elektrotlar, düşük alaşımlı ve karbon çelik boruların kaynağı için tasarlanmıştır. Bu ürünlerin benzersiz bileşimi sayesinde, her türlü yüke dayanıklı plastik dikişler sağlar.
Bu elektrotların tek dezavantajı, kenarların ön hazırlığı gerektirmesidir. Su, yağ veya pas ile temas halinde olan işlem görmemiş kenarlar, kaynak gözeneklerinin oluşumuna neden olabilir.
Kaynak makineleri
Kaynak yapmaya başlamadan önce, uygun ekipmanın kullanılabilirliği konusunda endişelenmeniz gerekir. En yaygın aparat, transformatördür, bunlar şebekedeki voltajı dönüştürmenize izin veren basit bir tasarıma sahiptir. Transformatörlerin çalışma prensibi, sargılar arasındaki ara akımdaki değişime dayanmaktadır. Kaynak transformatörleri% 90'a varan yüksek verimlilik ile karakterize edilir.
Daha gelişmiş bir tür kaynak ekipmanı bir redresördür. Bir diyot ünitesi, ayar, koruma ve başlatma elemanlarından oluşur. Pişirme sırasında transformatörlerin aksine, redresörler sadece siyahtan değil aynı zamanda demir dışı metal, dökme demir ve paslanmaz çelikten de parçaların birleştirilmesine izin verir. Redresörler ucuzdur ve kaliteli dikişler sağlar.
Dizaynı bir doğrultucu, bir transformatör, özel bir tahrik sistemi, brülörlü bir manşon ve bir gaz tüpü ile temsil edilen yarı otomatik cihazlar da kaynakçılar arasında büyük talep görmektedir. Kaynak gaz olmadan yapılırsa, ek olarak akı teli kullanılır. Genellikle metal boruları birleştirmek için aparat karbondioksit üzerinde başlatılır. Bu ekipmanın avantajı yüksek kaliteli dikiştir ve dezavantaj, yüksek malzeme tüketimidir.
İnvertörler de kendilerini iyi kanıtladılar. Bu tür ekipmanlara darbe denir. Pahalıdır, ancak düşük bir ağırlığa ve yüksek verimliliğe sahiptir. Ayrıca punta makineleri kullanarak kaynak yapmak için. Ekonomik, dayanıklı, güvenilir ve yüksek kaliteli sızdırmazlık sağlayan dikişler elde etmenizi sağlar.Ekipman, 0,01 sn olan akım darbeleri nedeniyle bağlantı elemanlarını anında ısıtır. Bu nedenle, minimum hacimde büyük hacimli bir kaynak işleminin yapılması gerektiğinde idealdir.
Dikiş çeşitleri
Hangi boru hatlarının amaçlanan amaçları için kaynatıldığına bakılmaksızın, önceden seçilmiş olan teknolojiye göre alternatif elektrik akımı ile oluşturulan kaynaklara sahiptir. Bugüne kadar, bir açıda dikişler vardır, kıstırma ve örtüşme. Hepsi kendi bireysel teknik ve özelliklerine sahiptir.
Popo eklemleri en yaygın olanıdır, çünkü metalin deformasyonundan yoksundurlar. Ek olarak, iç stresten asgari düzeyde tutulurlar ve dinamik ve statik yüklere göre yüksek mukavemete sahiptirler. Gövde derzleri, enine kesiti 600 mm'yi aşan borular için tasarlanmış, 500 mm'ye kadar ve enine kesitli borulara yönelik olarak tek parçaya bölünmüştür.
Köşe eklemleri bir popo besleme olarak kabul edilir. Parçaları bir açıda sabitlemek gerektiğinde seçilirler. Bu gibi dikişler iki şekilde elde edilir: bir eğim ve eğim kenarları olmadan.Köşe derzleri, alın derzleri kadar güçlü değildir, ancak yine de iyi kaliteye sahiptir. Çakışan dikişler plastik boruları yerleştirmek için harikadır. Metal elementleri kaynatırken nadiren kullanılırlar. Bu, bağlantının çok güvenilir olmadığı gerçeği ile açıklanmaktadır.
Kalın duvarlı boruları kaynak yaparken uzunlamasına bir dikiş kullanın. Birkaç katmandan oluşur ve iş, bir kural olarak, aynı anda iki uzman tarafından gerçekleştirilir.
araç
Kaynak, proseste katı bir boru hattı oluşturan bireysel elemanların birleştirilmesinin fiziko-kimyasal bir yöntemidir. Böyle bir kurulum, yüksek basınçlı plastik deformasyon veya füzyon kullanılarak gerçekleştirilir. Pişirme sırasında oluşan kaynak dikişleri, teknoloji seçimine bağlı olarak farklı olabilir.
Bugüne kadar, aşağıdaki kaynak türleri vardır:
- elektrik kaynağı;
- soğuk;
- gaz;
- argon;
- dağınık.
Boru pişirme yöntemleri arasındaki öncelik, elektrik kaynağıdır, düşük fiyat ve kullanım kolaylığı ile karakterizedir. Bu sözde iletişim yöntemidir. Bu şekilde bir bağlantı yapmak için, bir trafo veya invertör gereklidir.Ekipman, elektrotlara, boruların yüzeyi ile temas halinde olan, metali kuvvetli bir şekilde ısıtarak, daha sonra özel karışımlar veya su kullanılarak soğutulan bir şarj sağlar.
Elektrik kaynağının ana avantajları çok yönlülük ve çok yönlülüktür. Genellikle elektrotlar olmadan da yapılır. İkincisi kullanılıyorsa, boru kalınlığını ve boru kesitini dikkate alarak seçilirler.
Soğuk kaynak, belirlenmiş standartlar ve belgelendirme ile sıkı bir şekilde düzenlenir. Bu mühürlü mühürlü eklemler almak için en iyi seçeneklerden biridir. Bu teknik, kaynaklı elemanların ısınmasını tamamen ortadan kaldırmanıza olanak tanır ve dikişler, parça üzerine uygulanan deformasyon ve basınç işlemlerinden dolayı oluşur. Tekniğe bağlı olarak soğuk kaynak popo, dikiş ve punta kaynağına ayrılır. Bu yöntemin ana avantajı, tüm işlerin elektrik maliyeti olmadan gerçekleşmesidir. Buna ek olarak, teknik kesinlikle çevre dostu ve geniş alanlarda bileşikler oluşturmak için fırsatlar açıyor.
Genellikle farklı tip borular otomatik gaz brülörü ile bağlanır.Bu, metali yüksek sıcaklıklara ısıtan, oldukça eski ancak kanıtlanmış bir yöntemdir. Gaz kaynağı, montajı pürüzlü kaynakların elde edilmesinin yanı sıra kıç ayırma olmadan gerçekleştirmek için çok uygundur.
Aşağıdaki özelliklere sahiptir:
- yüksek verimlilik;
- işin sadeliği;
- kaliteli ve düzgün bir dikiş elde etmek.
Bağlanması zor olan malzemeleri örneğin alüminyum, bakır veya titanyum gerektiğinde argon kaynağı gereklidir.
Yukarıdaki tüm boru kaynak teknikleri metal malzemenin birleştirilmesi için uygundur, plastik parçalar ise dağınık kaynak kullanılarak kaynaklanır. Uygulaması minimum araç seti gerektirir, iş hızlı ve ucuzdur. Hermetik dikişleri elde etmek için hazırlık yapılır, ardından lümene karşı plastik borular farklı nozullarla donatılmış özel bir cihazla ısıtılır. Her nozul belirli bir boru çapı için seçilir. Özel teknikler ve teknolojiler sayesinde boru parçaları özel bir cihaza yerleştirildiğinde ve mekanik olarak 360 derece döndürüldüğünde, orbital kaynakların etkili bir yöntem olduğu düşünülmektedir.Sonuç, boşluklar olmadan düzgün bir dikiştir.
Kusur ve evlilik nedenleri
Yüksek kaliteli boru erimesinin bir göstergesi, kaynaklarda kusur olmadığı kabul edilir. Bu özellikle ulaşılması zor yerlerde bulunan ince duvarlı ve sıhhi tesisat ürünleri için geçerlidir. Kaynak elle yapılırsa, kalitesine büyük önem vermek önemlidir, aksi halde herhangi bir hata, tüm yapının mukavemetinde veya tahribatında azalmaya yol açabilir.
Kaynaklı eklemlerin kusurları aşağıdaki tiplere ayrılır:
- katı kapanımlar;
- dikiş dış formlarının distorsiyonu;
- çatlaklar;
- kraterler, fistüller, kaviteler.
Çatlaklara genellikle sütürün yakınındaki yerel bir kırık neden olur. Metalin tabanına veya sıcaklık maruziyetine yerleştirilirler. Böyle bir evliliğin ortaya çıkmasının nedeni, pişirme sırasında eklemlerde ortaya çıkan yüksek voltajdır. Çoğu zaman, çok çabuk soğuduktan sonra alaşımlı ve yüksek karbonlu çelikten yapılan kaynatma boruları arızalı çatlaklar görülür.
Diğer taraftan kaviteler, köşeleri olmayan keyfi şekil oluşumlarıdır. Kaynak sırasında, ısıtılmış metal içine sızarlar.Çeşitleri fistül ve kraterler. Bu tür kusurlar, kaynak yüzeyi bölgesinde kirlenme, boya veya pas bulunduğunda ortaya çıkar.
Kuru ham elektrotlar kullanıldığında reddetmeler de meydana gelebilir. Gözenekler genellikle yanlış kaynak teli seçimi ile görülür.
Katı kapanımlar söz konusu olduğunda bunlar, kaynak sonrası kaynak metali içinde kalan farklı kökenden yabancı elemanlardır. Bunlar oksit, akı ve cüruftur. Kapsamalar farklı şekillerle karakterize edilir ve çoğunlukla yön ve baz metalin sınırında bulunur. Bu kusurlar, yüksek pişirme hızının, boruların yüzeyindeki kirlerin varlığında veya elektrotların kaplama malzemesinin dökülmesinin bir sonucu olarak elde edilir.
Bazen "penetrasyon eksikliği" denilen söz konusudur, metal ve dikiş arasında hiçbir bağlantı yoktur. Bu tür kusurlar genellikle dikişin kökünde, yan yüzeyinde veya silindirler arasında gözlemlenir. Bu türden bir evliliği önlemek için, kenarları dikkatlice temizlemeli ve cihazın hızını kontrol etmelisiniz. "Kötü penetrasyon" a ek olarak, ortak bir sorun, alt kesimlerin görünümü olan dikiş şeklinin ihlalidir.Bu problem, yüksek voltaj ve pişirme hızından kaynaklanmakta ve bir "kambur" eklem ile sonuçlanmaktadır.
Elektrot eğimi yanlış seçilmişse ve geniş bir ark uzunluğu kullanılıyorsa, bu bir “akı” neden olabilir. Bu durumda dikiş, füzyona sahip değildir, çünkü metal, yer çekimi eylemi altında düzgün bir şekilde dağılmamış ve yatay rafa sızarak, incrustasyonlar meydana getirmektedir.
Kaynakta diğer kusurlar şunlardır: sıçrayan ve metal inceltme, rasgele ark ve harici teaser. Bazik metal ile temas halinde elektrotların kısa bir devresi oluştuğunda rastgele bir ark ortaya çıkar. Sıçramalar, kaynak akımı talep edildiğinde oluşan katı damlacıklar biçimindeki kusurlar olarak kabul edilir. Müttefikler, eklemlerin belirlenmiş boyutlarına ve genişliğine uymayan derzlerde düz olmayan yüzeylerdir. Kaynak telinin kayması ve sıvı metalin boşluklara akmasıyla oluşurlar.
Yukarıda listelenen tüm kusurlar ortadan kaldırılmalıdır. Bunu yapmak için ultrason veya radyografik izleme kullanılarak tespit edilir ve bir dizi aktivite gerçekleştirilir.
Polipropilen boruları kendiniz lehimlemek için aşağıdaki videoya bakınız.